Case Study: Functional mechanical components printed from Prusament PC Blend
It’s been a while since we launched our polycarbonate filament. We developed our own “recipe” and tested it in the Prusa Polymers laboratory. It took a lot of effort to fine-tune and experiment because we wanted to create a material that would have all the qualities of polycarbonate, but also good printability. And that was the birth of the Prusament PC Blend!
Material:
- Prusament PC Blend
3D model:
- mechanical model of the compounding line motor coupling
Requirements:
- deformation-resistant, durable material
- able to withstand a combination of higher temperatures and mechanical stress
A real stress test
During the final tests of the material, just before the planned launch of the filament, we had an unexpected opportunity to test it in practice: A part of the motor powering our compounding line was damaged. Delivery of the new part was expected to take 14 days and since the compounding line is used on daily basis, such a delay was unacceptable. The solution was obvious – to make the line operational again, we will replace the damaged metal part with a new one printed from Prusament PC Blend on one of our Original Prusa 3D printers. This will be a real stress test!
First, our designer prepared a 3D model of the required coupling of the electric motor and processed it for 3D printing. The part of the model has been divided into two parts for better printing and assembly.
We chose Prusament PC Blend Natural for printing the parts. They were printed on the Original Prusa i3 MK3S printer (without an enclosure) with a layer height of 0.2mm with a rectilinear infill of 20% density. The more advanced slicer settings were the same as they are now in the current profile in PrusaSlicer. Simply select the material default preset: Prusament PC Blend to print your parts from Prusament PC Blend and you are good to go.
3D printed coupling
The finished 3D model was used as a motor coupling for compounding line mixing (compounding) granulate. The transmitted torque had been higher than 55 Nm for 3 weeks – and the model passed the test with flying colors! After we received a new part from the manufacturer, it was possible to replace the printed substitute. The condition of the used coupling can be seen in the photo. In addition to the 3D printed part, there is also the entire component of the electric motor.
Stress tests with excellent results
Avoiding downtime with a quick replacement of the component is definitely the main advantage. Obviously, having the compounding line out of operation for a longer period would hamper our research and production.
Prusament PC Blend passed the practical test with excellent results, as a material suitable for heavy-duty mechanical loads.
What are the benefits of PC Blend and when is it worth using it?
We chose Prusament PC Blend for its ability to withstand a combination of higher temperatures and mechanical stress without deformation (i.e. “creep resistance”). In general, Prusament PC Blend is the perfect choice for strong and durable 3D prints or mechanically stressed parts. PC Blend is highly heat resistant, up to 113 °C. Naturally, we also focused on the good printability on our Original Prusa i3 MK3S printers. Therefore, Prusament PC Blend is easy to print even without an enclosure.
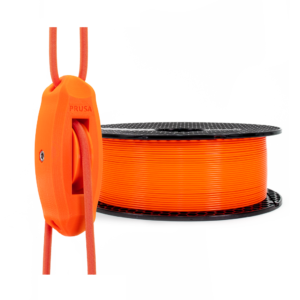
Go to the e-shop.