Chemical resistance of 3D printing materials
With growing interest in 3D printing, there are new materials coming to market – and with them new means and opportunities for using 3D printers. It’s common for prints to be used in outside conditions where they need to withstand wind and rain, UV light – or in industry – withstand harsh mechanical stress. Often prints are exposed to various chemicals.
That is why we have decided to explore the chemical resistance of printing materials in detail. We’ll show you chemically resistant polymers and you’ll learn how exposure to chemicals affects material durability.
Prusament PLA, PVB, PETG, ASA and PC-Blend were exposed by various chemical substances: We chose those which are common and safe to work with.
We believe that our tests will help you choose the right material fitted for your needs.
Where are chemically resistant materials used?
Material’s ability to resist certain chemicals is very important in industry: In manufacturing and automotive, end-products are often exposed to many aggressive materials. Part for manufacturing lines are commonly in contact with lubricants and cleaning products. Car components are – apart from lubricants and oils – exposed to maintenance substances.
Pharmaceutical and food industry require chemical stability of used materials. And because new filaments are resistant and stable, you’ll also find use for 3D printing and printed parts in these industries.
Chemical resistance of polymers
Chemical resistance is the ability of material to resist when exposed to a chemically aggressive environment. Today, a wide spectrum of polymers exists that is able to resist acids, solvents, alcohol or hot water and other substances. This article will cover the most commonly used polymers for 3D printing – and are mostly suitable for using under demanding circumstances.
Key factors that affect chemical resistance of polymers
Molecular structure of the polymer
The chemical resistance of plastics depends primarily on the physical and chemical structure of the polymer and the chemical composition of the substance. Polymers used for 3D printing have chains formed as either an amorphous (disordered) or semi-crystalline (partially ordered) phase after cooling. In semicrystalline, ordered segments are surrounded by disordered clusters of chains. The ratio of these segments (referred to as crystallinity) affects the temperature resistance, strength and toughness of the polymer. It also affects the polymer’s resistance to chemical aggressiveness. Thus, a more crystalline polymer is more resistant to an aggressive substance than a less crystalline polymer. The orientation of the polymer bonds and the presence of fillers in the material may also have an effect.
The ability of a material to withstand a chemically aggressive environment depends not only on its chemical resistance, but also on other factors that stress it: that includes mechanical stress, physical absorption of the substance by the material, or temperature. These parameters can significantly influence the requirements for material selection.
If the material is not chemically resistant, there is a risk of rapid degradation of its polymer bonds when in contact with an aggressive substance. The consequence is lower tensile strength, lower impact toughness and shorter material life – which all can result in component failure.
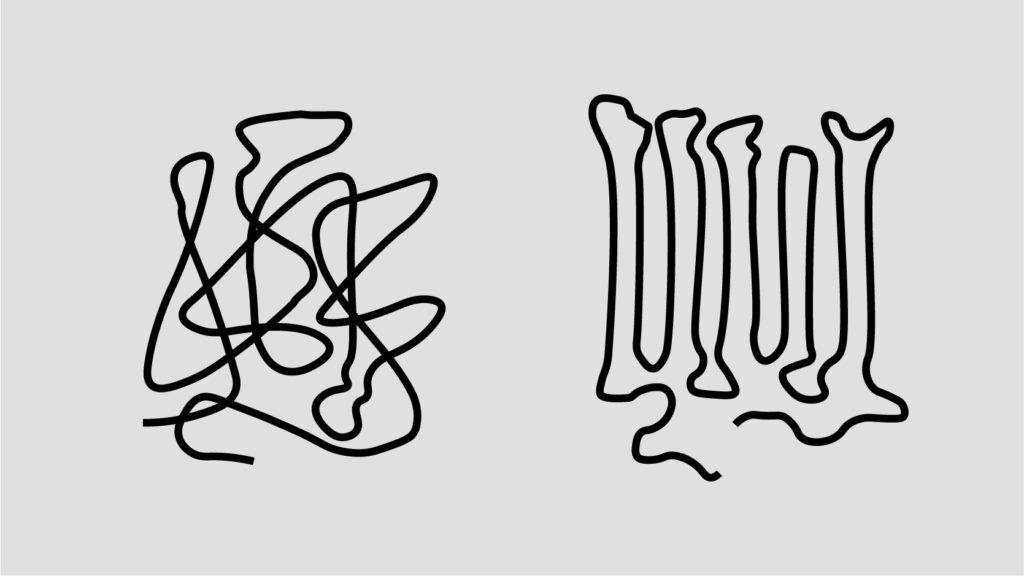
Absorption of the substance
When a polymer undergoes a chemical reaction, the structure of the polymer chain is affected. When a substance is physically absorbed by the polymer, the chain is not affected, but the substance is absorbed into the plastic resembling a sponge soaking up water. Internally, the chemical can cause changes in the weight, mobility of the polymer chains and dimensions of the plastic component. This can also manifest itself as softening or, conversely, embrittlement of the plastic.
Temperature
Most diffusion processes are temperature dependent. In practice, this means that the chemical degradation of polymers increases exponentially with higher temperature of the substance. In general, the higher the temperature of the substance, the lower the resistance of the material to the environment. For example, it can be observed that the same material is more resistant in cold water than in hot water at the same concentration and length of exposure.
Concentration of chemical substance
In most cases, increasing the concentration of the active substance accelerates the degradation of the polymer.
Mechanical stress acting on the material
Mechanical stress is an important factor when exposed to chemically aggressive environments. Loading a material in a chemically aggressive environment can lead to the breaking of covalent bonds, even though the load is below the yield strength of the material. Cracks are formed which further penetrate into the depth of the material, which can lead to integrity failure.
3D model design
Another important parameter in 3D printed models is the design and quality of the printed model. Corrosive substances can penetrate through the printed object and significantly reduce its lifetime. Therefore, it is essential to choose the right material and printing parameters for the model.
Chemical resistance of commonly used 3D printing materials
In general, engineering materials are the most resistant to chemicals: Those with excellent chemical resistance include PP (polypropylene), PA (polyamide, nylon), PE (polyethylene), PEEK (polyetheretherketone), PTFE (polytetrafluoroethylene, Teflon), PVC (polyvinyl chloride), or PVDF (polyvinylidene fluoride).
Materials with good chemical resistance include PC (polycarbonate), TPU, PETG, ASA, or ABS. However, the resistance of these materials depends on the specific environment, the ambient temperature and other types of stresses. For example, ABS material degrades very quickly in acetone.
Materials that do not have technical characteristics – such as PLA, PVB – are not suitable for use in chemically aggressive environments – acids, alcohols, etc.
Table of chemical compatibility of plastic materials and their chemical resistance
Below is an indicative table of the most commonly used polymers for 3D printing that have been tested in various chemicals. According to the resistance rating from A to D, it can be determined which polymer is suitable for use in a given substance. The tests were carried out at 23 °C.
* Fridex is the industry name for a chemical compound used in antifreeze coolants for automobiles. It is a concentrated coolant based on ethylene glycol.
** Savo is a cleaning and disinfecting agent. The disinfectant is sodium hypochlorite, 4.7 g / 100 g.
Rating:
A – Resists very well. Polymer does not melt, absorb substance, or swell during a week’s immersion (less than 1% change in weight and dimensions).
B – Resists moderately to well. Slight swelling or change in weight (2 – 3% change in weight or dimensions).
C – Resists poorly. Significant swelling and change in weight of the test sample (4-5% change in weight or dimensions) occurs with prolonged exposure of the polymer.
D – Does not resist. A red colour indicates a significant change in weight, severe swelling (change in weight or dimensions over 5%) or complete destruction of the fibre (2).
Data for the evaluation of polymers were obtained from our measurements under laboratory conditions and from a scientific publication (1)
More extensive laboratory testing is required for more accurate analysis of the results. The durability of the material and its chemical resistance is influenced not only by the substance itself, but also by environmental influences such as temperature, concentration of the substance, mechanical stress on the component and other factors mentioned above.
Chemical resistance tests of Prusament PLA, PVB, PETG, ASA, PC Blend
The resistance of each material varied depending on the chemical composition of the environment to which it was exposed. The effect of the environment on the resistance of the material was measured. Two properties of the material – its strength and toughness – were compared in more detail.
Testing process
More than 400 test specimens were printed for each material, subjected to chemical loading and then subjected to Charpy tensile strength and impact strength measurements. Tensile strength was measured according to ISO 527 on a universal testing machine. Impact toughness was measured in accordance with ISO 179.
The model of the test bodies was generated by the PrusaSlicer program. The G-code contained the print settings for the Prusament material profile for the given material – namely Prusament PLA, Prusament PETG, Prusament ASA, Prusament PC Blend and Prusament PVB, infill 100%, 2 perimeters, layer height 0.2 mm. The orientation of the model on the printing pad was in the XY axis.
All the materials were tested in nine substances, which showed different chemical compositions – water, ethanol (EtOH), isopropyl alcohol (IPA) 75% and 99%, vinegar 8% (the main component of which is acetic acid), table salt (NaCl) 10%, citric acid (C6H8O7), Fridex (ethylene glycol) and Savo (containing sodium hypochlorite as an active ingredient. Mixed with water in a 1:10 ratio).
Exposure of the chemical environment to the material was carried out at room temperature of about 23° at four-time intervals – 1 hour, 7 hours, 24 hours and 7 days.
Test results
The data obtained from tensile strength and impact strength measurements are shown graphically. The values obtained have been converted into percentages – it is, therefore, possible to see how the material properties change depending on the exposure time and chemical environment. The increase or decrease in chemical resistance in a particular environment can be tracked by the percentage changes on the graphs. To compare the change in strength or toughness of the material with the baseline value, a test sample (called a standard) that has not been exposed to any chemical is shown on each graph. The printing of the standard was carried out under the same conditions.
PLA
Tensile strength:
Initial value: 55 MPa = 100%
According to the values in the graph, it can be observed that the tensile strength of PLA decreased slightly in contact with water. The decrease in strength was more pronounced in more aggressive environments. A rapid decrease in strength was recorded in contact with Fridex (ethylene glycol) after 1 hour. A gradual decrease in strength occurred with contact with IPA after more than 24 hours. When the PLA material was immersed in acetone, the test body collapsed.
Impact toughness (according to Charpy):
Initial value: 15 kJ/m2 = 100 %
The impact toughness of PLA was slightly higher when in contact with less aggressive environments. A more pronounced decrease in toughness occurred with exposure in Fridex (ethylene glycol) and Savo.
PVB
Tensile strength:
Initial value: 52 MPa = 100 %
The PVB material proved to be highly absorbent and thus its strength was affected. For the less aggressive materials, there was no rapid decrease in strength, but the trend showed that strength decreased with time. On contact with the substances Ethanol, IPA, Acetone the test body softened and partially dissolved after 1 hour, after longer exposure it collapsed. These substances were not resisted by the PVB, therefore it was not possible to measure the samples.
Impact toughness (according to Charpy):
Initial value: 54 kJ/m2 = 100 %
The PVB material showed low chemical resistance and significant wetting. This resulted in an increase in impact toughness in all tested fabrics. The substances Ethanol, IPA and Acetone completely disrupted the structure of the test bodies. Again, the test samples were unusable for further measurements after only 1 hour of exposure.
PETG
Tensile strength:
Initial value: 47 MPa = 100 %
For PETG, the tensile strength changed significantly on contact with acetone. Across the other substances, the strength deviates by a few percent. More significant changes occurred after longer exposure times. During exposure to the substance for 7 days, the strength of the test body immersed in ethanol, IPA 75% and IPA 99%, acetone decreased.
Impact toughness (according to Charpy):
Initial value: 65 kJ/m2 = 100 %
The impact toughness of PETG remained almost unchanged only in contact with water. When in contact with Savo, the toughness value remained almost the same after 24 hours. However, it decreased with longer exposure time and dropped to values around 92%. For the other substances there was a significant decrease in toughness. For IPA, vinegar, acetone and Fridex the decrease in toughness is most pronounced.
ASA
Tensile strength:
Initial value: 42 MPa = 100 %
The ASA was resistant to substances such as water, citric acid, Fridex, Savo, even with prolonged exposure time. More significant decrease in tensile strength occurred in ethanol, IPA 75% and IPA 99%. In acetone, the test body collapsed, therefore, the measurement could not be performed.
Impact toughness (according to Charpy):
Initial value: 25 kJ/m2 = 100 %
The impact toughness of ASA decreased when used in chemically aggressive environments. According to the graph we can compare the loss of toughness, which was most pronounced for NaCl 10% after 24 hours of exposure. However, the opposite is true for the toughness values measured for samples exposed to ethanol, IPA 75%, or citric acid, where the toughness was almost maintained relative to the value of the test sample (standard). The ASA material does not resist acetone, so here too the test body collapsed during exposure.
PC Blend
Tensile strength:
Initial value: 63 MPa = 100%
PC Blend proved to be a strength-stable material, but is poorly resistant to acetone. The strength dropped significantly on contact with acetone after 24 hours and the strength loss was more pronounced with longer exposure.
Impact toughness (according to Charpy):
Initial value: 110 kJ/m2 = 100 %. Charpy 100/100. It can therefore be stated that the impact strength of the test specimen is higher than 110 kJ/m2.
The value 100% in the graph indicates the maximum measurable energy for breaking the test body (standard). In practice, this means that the standard and other test bodies with a value of 100% withstood a hammer impact of 4 J without breaking or significant damage. Taking into account the dimensions of the specimen, it can be argued that the impact strength of the specimens with a value of 100% is higher than 100 kJ/m2.
Conclusion
Prusament PC Blend is one of our most chemically resistant materials. Its excellent properties are confirmed by chemical resistance tests. The tensile strength of PC Blend is higher than that of other materials and does not drop significantly even when the printed parts are exposed to selected chemicals. The impact strength of PC Blend is significantly higher, which the material can maintain even in chemically demanding environments.
From the measurement results, we can compare how the impact of the chemical affects the strength and toughness of the material.
Of the materials tested, PC Blend clearly stands out as the toughest material even after detailed testing.
For more information about our materials, please visit our website prusament.com.